The method of discovering and exploring data is an efficient way to find intelligent results for the most different sectors of the industry. Banbury mixer, an industrial equipment, is designed to carry out intensive compound mixing with high performance and precision. With sensors and monitoring systems, it is possible to collect data such as torque, temperature, and mixing time, allowing for real-time adjustments to optimize the process and ensure consistency.
Its operation is based on a closed mixing chamber, where two rotors rotate in opposite directions, promoting intense shear of the material. This movement, combined with temperature and pressure control, favors the efficient melting and dispersion of components. The heat generated by friction softens materials such as rubber, making it easier to incorporate additives.
Designed to handle large volumes, Banbury stands out for its repeatability of the process, which, with the support of data analysis, becomes even more reliable and efficient.
When analyzing information about the Banbury Mixer, data science is a great ally to further optimize your process, based on several types of analysis:
- Rheological analysis: evaluates how materials flow in the Banbury mixer, allowing you to identify the impact of process conditions on viscosity and elasticity;
- Shear analysis: monitoring variables such as temperature and pressure helps in the dispersion of materials such as polymers in opposite directions;
- Analysis of key process variables: evaluates factors such as temperature, pressure, and mixing time to understand their impact on the mechanical properties of the elastomeric compound;
- Energy efficiency analysis: evaluates how energy consumption impacts the product quality and efficiency of the Banbury mixer, being crucial in both production and processing.
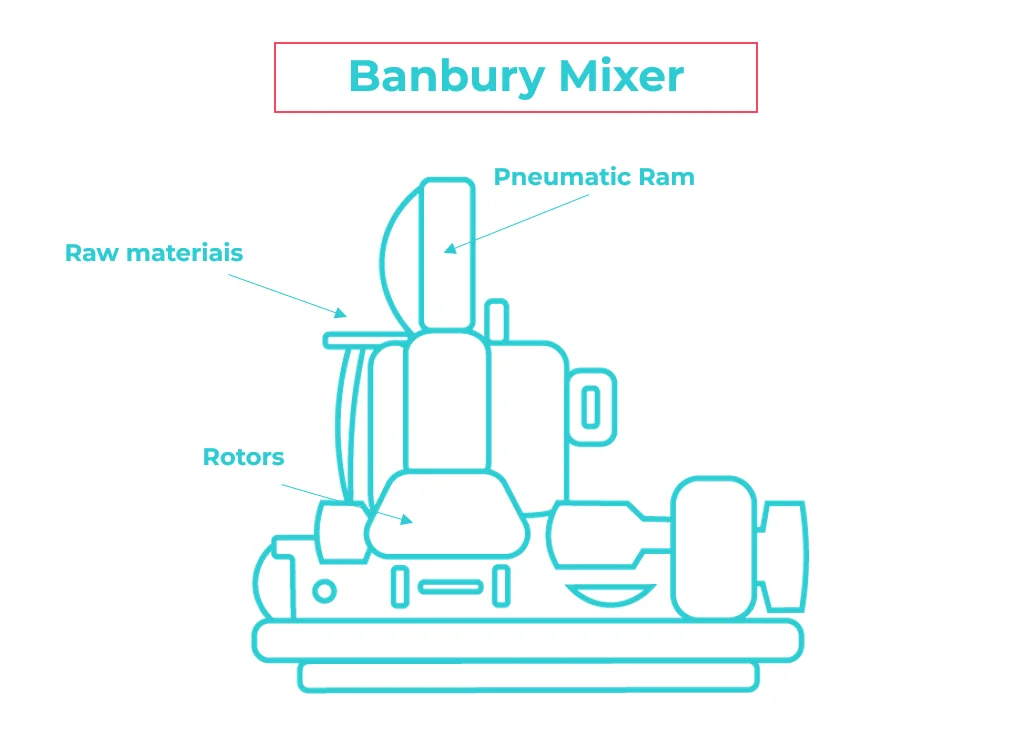
Thus, the analysis that is applied to the Banbury mixer is valid for several types of industry, such as:
- The Banbury mixer, in the chemical industry, mixes raw materials, generating heat by friction, with generally exothermic processes, although some mixtures absorb heat and cool.
- In the polymer industry, the Banbury mixer ensures the uniform distribution of the heat required for vulcanization, a process that increases the durability of the material through cross-linking between polymer chains.
- In the cosmetics industry, the Banbury mixer mixes ingredients, pigments and additives, while energy efficiency analysis optimizes quality and energy management.
Development of other materials with Banbury
Academic and industrial research has explored the use of the Banbury Mixer to create composites, nanocomposites and blends with enhanced properties. This includes the incorporation of additives in thermoplastics and elastomers for scientific and technological projects, requested by industries and academic research.
Another study in this area is from the Federal University of Rio Grande do Sul (UFRGS), produced in 2010. The dissertation highlights fundamental variables in the mixing process in internal mixers such as Banbury, especially in the context of elastomeric compounds.
Variables, such as the degree of filling, the discharge temperature, and the ingredient introduction times, directly influence the dispersion and homogeneity of materials, affecting their mechanical and rheological properties. Understanding these parameters is essential for optimizing the quality of compounds and meeting industrial standards.
In addition, an online mini-course, produced in 2015 by researchers from the Federal University of Campina Grande, is available on ResearchGate. The available material addresses the processing of polymers in the Laboratory Internal Mixer, including academic and industrial applications.
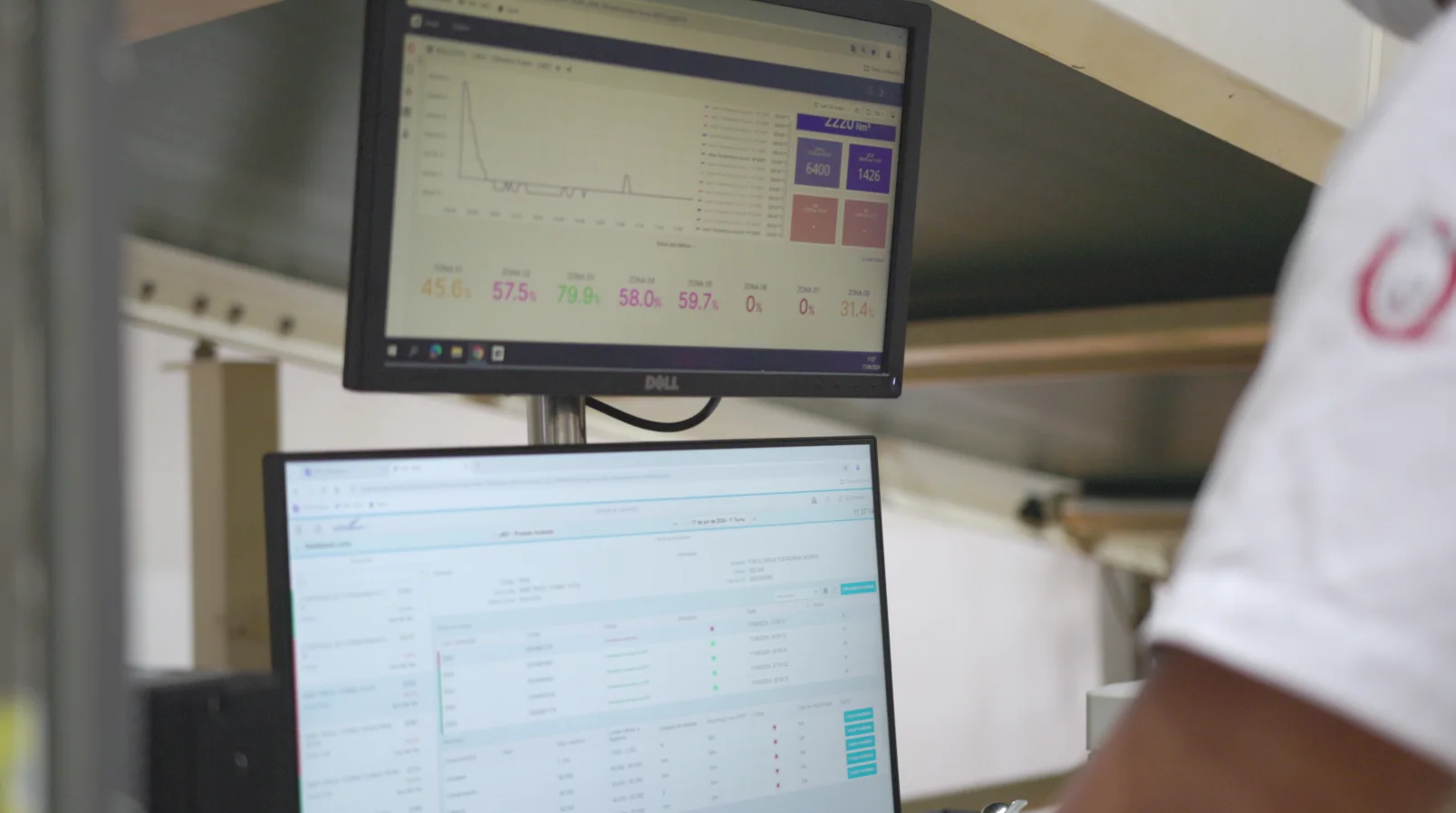
In addition to the applications mentioned, the Banbury mixer is also present in the PVC transformation industry for the furniture industry, especially in the formulation stage of flexible compounds. During this phase, all formulation ingredients — such as PVC resins, plasticizers, thermal stabilizers, fillers, and pigments — are homogenized using intensive mixers.
The control of the operational variables of this type of mixer is essential to ensure the quality of the final compound. Among the most relevant variables are: mixing temperature, processing time, rotor speed, applied torque, piston pressure (ram) and the feeding sequence of the components.
These parameters directly influence the physical and chemical properties of the compound, such as viscosity, degree of dispersion, and thermal stability. The following is a table with the main variables associated with the mixing process at Banbury:
Variable | Description | Importance |
Mixing Temperature | Internal temperature of the chamber during the process | Prevents thermal degradation and improves mix quality |
Mixing Time | Total Mixing Cycle Duration | Controls homogeneity; Excessive time can damage materials |
Rotor Speed (RPM) | Rotation of the rotors during mixing | Influences the shear force and dispersion of ingredients |
Torque | Resistance of the rotors to movement during the process | Indicates the viscosity and consistency of the mixture |
Ram pressure (plunger) | Pressure exerted on the materials inside the chamber | Ensures effective contact with the rotors and better mixing |
Feeding sequence | Order and time for adding ingredients | Affects chemical reaction and uniform dispersion |
In short, the analysis of energy efficiency in Banbury mixers brings several optimizations with advanced technology, digitalization of the production line and assertive data collection. In addition, they have a significant impact by influencing the mechanical and rheological properties of the compound, which directly affects the quality of the product.
Learn more about ST-One