Industrial ovens are fundamental parts of production in various industries, from metallurgy to baking, playing essential roles in the transformation of materials through heat. Each type of furnace has its own characteristics, designed to meet the specific needs of your industry.
In metallurgy and steelmaking, induction furnaces use electromagnetic fields to melt metals efficiently, ensuring thermal uniformity and structural quality. Controlling the frequency of the electromagnetic field and temperature is essential to maintain uniformity in heating, avoiding deformations or structural failures. In the ceramic and glass industry, high-temperature furnaces operate above 1600°C, allowing fusions and glazing, essential for the strength and durability of the products. To maintain production quality, it is common to monitor internal pressure and temperature.
In the chemical and pharmaceutical sector, electric ovens provide precise temperature control, ensuring safe sterilizations and stable chemical processes. Energy efficiency is crucial here, monitored through electrical consumption and thermal stability.
The food and bakery industry depends on ballast ovens, which, with their refractory stones, ensure uniform cooking and optimal texture in breads and confectionery. Controlling stone temperature and humidity is essential for the final quality of products.
On the other hand, gas furnaces are widely used in the production of metal alloys and in the sintering of ceramics, standing out for their rapid reach of high temperatures and thermal efficiency. Gas flow and temperature are monitored to maximize combustion and performance.
Tunnel Oven in the Food Industry: Control and Continuous Improvement
In the food industry, large-scale production requires continuous, standardized, and controllable thermal processes. The tunnel oven is a central piece in this scenario, especially in biscuit production lines, where it connects the dough shaping to the final packaging.
The process begins with the molded dough being transported by a conveyor belt through the oven, divided into thermal zones with specific functions.
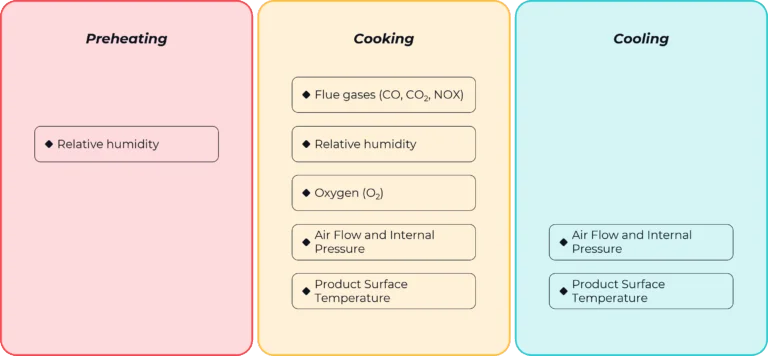
The first is the preheating zone, which gradually raises the temperature of the product, promoting the evaporation of surface moisture and preventing thermal shocks that could affect the structure of the cookie. Humidity control here is essential to preserve the integrity of the dough.
Then comes the cooking zone, where the main physicochemical transformations occur: starch gelatinization, gas expansion, evaporation of internal water and crust formation. This zone is subdivided with individual upper and lower temperature control, allowing adjustments according to the type of product. In gas furnaces, sensors monitor flue gases and oxygen to ensure safety and efficiency. Airflow and pressure sensors maintain thermal uniformity, ensuring standardization.
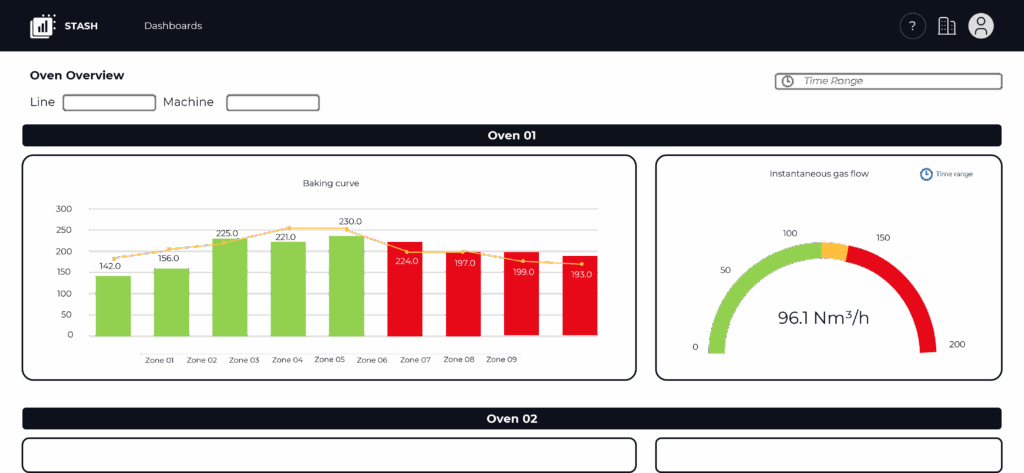
After baking, the biscuits pass through the cooling zone, which reduces the temperature in a controlled manner to prevent condensation and deformation. Cooling can be natural or forced, and sensors ensure that the cookies reach the ideal temperature for packaging.
The efficiency of the tunnel furnace depends on the collection of assertive variables, PID control and real-time data analysis, which enables energy optimization, predictive maintenance and quality traceability.
Each step of the tunnel kiln plays a strategic role, from dough preparation to final cooling, ensuring a standardized, high-quality product.
Tunnel oven in the ceramics industry: from sintering to dimensional quality
In the ceramics industry, the manufacture of sanitary ware such as basins requires a rigorous and continuous thermal process. The continuous tunnel kiln is the central equipment, leading the parts through a complete cycle — from final drying to glazing — ensuring dimensional stability, mechanical strength and good surface finish.
The raw parts are loaded onto carts that slowly travel through the inside of the kiln. The first stage, preheating, raises the temperature gradually to about 600 °C. In this phase, residual moisture is removed and decomposition reactions of organic compounds occur. Controlling the heating rate, relative humidity and exhaust of volatile gases is essential to avoid cracks, fissures and deformations in parts.
Then, the parts enter the firing zone, where the temperature reaches 1200 °C to 1250 °C. This is where the main transformations take place: the sintering of the ceramic mass and the glazing of the glaze. This zone is segmented with independent control points, using sensors to monitor temperature, airflow, internal pressure, and flue gas composition (CO, CO₂, NOx). Oxygen probes optimize burning efficiency, especially in gas furnaces. The speed of the carts is adjusted according to the required thermal profile, ensuring optimal residence time.
In the final step, controlled cooling reduces the temperature of the parts to about 100 °C, gradually, avoiding thermal shocks that could compromise structural integrity. Flow-controlled fans and temperature sensors ensure parts reach safe conditions before they leave the furnace.
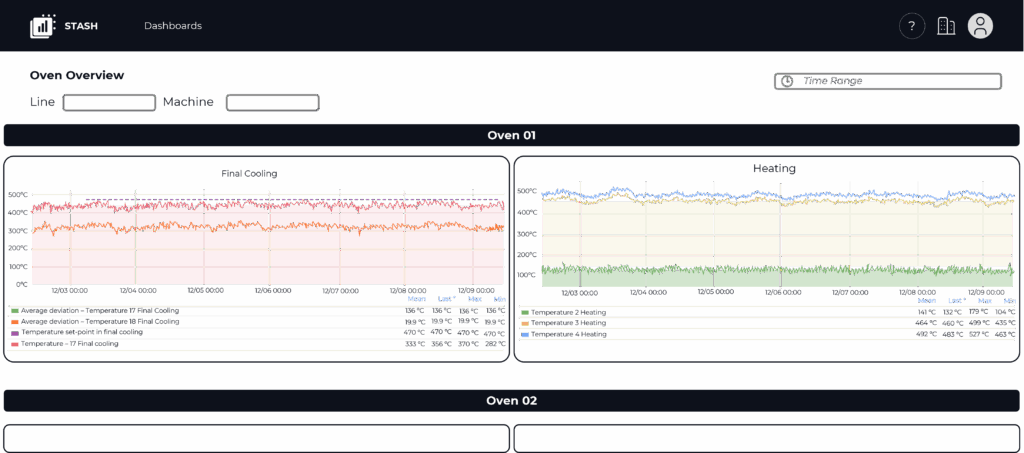
Thermal curve, atmosphere and energy: parallels between ovens in the food and ceramics industry
Despite differences in temperature, residence time, and nature of the products processed, the food and ceramics industries share common technical fundamentals in process engineering, quality control, and operational efficiency, enabling integrated analytics and similar optimization strategies.
One of the central aspects is the development of the thermal curve and the heating profile. In both cases, modeling and controlling the thermal curve is essential to maximize energy efficiency and reduce defects. Tools such as thermal simulations, temperature gradient analysis, and distributed PID control are widely applicable, with the common goal of ensuring that the product achieves critical transformation parameters — whether it’s food cooking or ceramic sintering — without structural failures.
Typical Thermal Curves in Tunnel Ovens: Biscuits vs Sanitary Ware
Another fundamental point is the thermal distribution and its uniformity throughout the furnace. The homogeneity of the thermal environment is evaluated through mapping with distributed sensors, use of infrared cameras and CFD (computational fluid dynamics) simulations. This analysis reduces quality variations between different kiln positions or between batches, promoting greater standardization.
Energy efficiency is also a shared goal. The measurement of consumption per unit of product, associated with the analysis of thermal losses and strategies such as heat recovery, allows reducing operating costs and emissions, even in the face of different thermal scales.
Finally, the control of the furnace’s internal atmosphere is critical in both sectors. Monitoring the composition of gases — such as O₂, CO, CO₂ and relative humidity — avoids unwanted reactions, such as oxidation or drying out, and ensures the stability and repeatability of the production process.
Control in industrial oven and ESG: efficiency and responsibility
According to CNN Brasil (2024), investments focused on ESG — environmental, social, and governance criteria — already represent more than a third of global assets under management, with projections pointing to US$ 53 trillion by 2025. Companies that underperform on these criteria face difficulties in attracting investors, since ESG reports are used as a key reference in investment decisions. Data from SAP reinforces this trend: in 2022, 69% of large industries in Latin America already had ESG strategies in place.
In this context, the analysis and control of variables in industrial furnaces, especially temperature, play a strategic role. In the Environmental pillar, precise temperature control contributes directly to energy efficiency, reducing fuel consumption and, consequently, emissions of gases such as CO and CO₂. This favors compliance with environmental standards, such as ISO 14064, and reinforces the commitment to sustainable practices.
In the social aspect, the safe and stable operation of the furnaces reduces the risk of accidents, overheating and failures that can compromise both the integrity of employees and the quality of the product. Compliance with standards such as ISO 9001 strengthens the company’s reputation with customers and partners.
In governance, continuous monitoring of thermal variables and transparency in the disclosure of operational data are fundamental. Reports aligned with standards such as GRI and SASB demonstrate corporate responsibility and reinforce stakeholder trust.
Analyzing thermal variables in industrial furnaces, therefore, goes far beyond operational efficiency: it is a central practice in building a more sustainable, safer, and transparent industry.