Los Controladores Lógicos Programables (CLPs), concebidos en los años 60 en EE. UU. para reemplazar los complejos sistemas de control electromecánicos, entonces predominantes en la industria automotriz, emergieron como una solución disruptiva. General Motors lideró su adopción, buscando agilidad y robustez operativa. El Modicon 084 inauguró la era comercial, permitiendo la reconfiguración lógica vía software, eliminando intervenciones físicas. Desde entonces, la continua evolución de hardware y software consolidó a los CLPs como elementos esenciales en la automatización industrial contemporánea.
La programabilidad define la capacidad central de los CLPs, proporcionando adaptabilidad dinámica mediante lógica personalizada en software. Su robusta arquitectura integra una CPU de alto rendimiento para el procesamiento veloz de tareas complejas, módulos de E/S para la adquisición de datos concurrente y el control preciso de periféricos, fuentes de alimentación resilientes para una operación ininterrumpida e interfaces de comunicación versátiles para la integración sistémica y la escalabilidad.
La heterogeneidad de protocolos en plantas industriales deriva de la evolución tecnológica y la proliferación de máquinas especializadas. Estándares como OPC-UA y MQTT, superiores en flexibilidad e integración a sistemas legados como Modbus y RS232, ganaron adopción. La especialización de maquinaria introdujo protocolos optimizados, como Fanuc CNC, y propietarios, como Mitsubishi Melsec. Esta coexistencia de distintos protocolos dentro del mismo entorno productivo subraya la necesidad de interoperabilidad.
La flexibilidad comunicacional ofrece ventajas estratégicas cruciales: interoperabilidad irrestricta en la selección de equipos; escalabilidad facilitada por la adición de nuevos dispositivos con mínima reconfiguración; adaptabilidad ágil a tecnologías emergentes e IoT; integración fluida con sistemas corporativos (como Historian) para la optimización operativa; y robustez de la seguridad mediante protocolos avanzados que aseguran la integridad y protección de los datos industriales. En resumen, la capacidad de comunicación multi-protocolo es fundamental para la eficiencia, la escalabilidad y la seguridad de las operaciones de manufactura modernas.
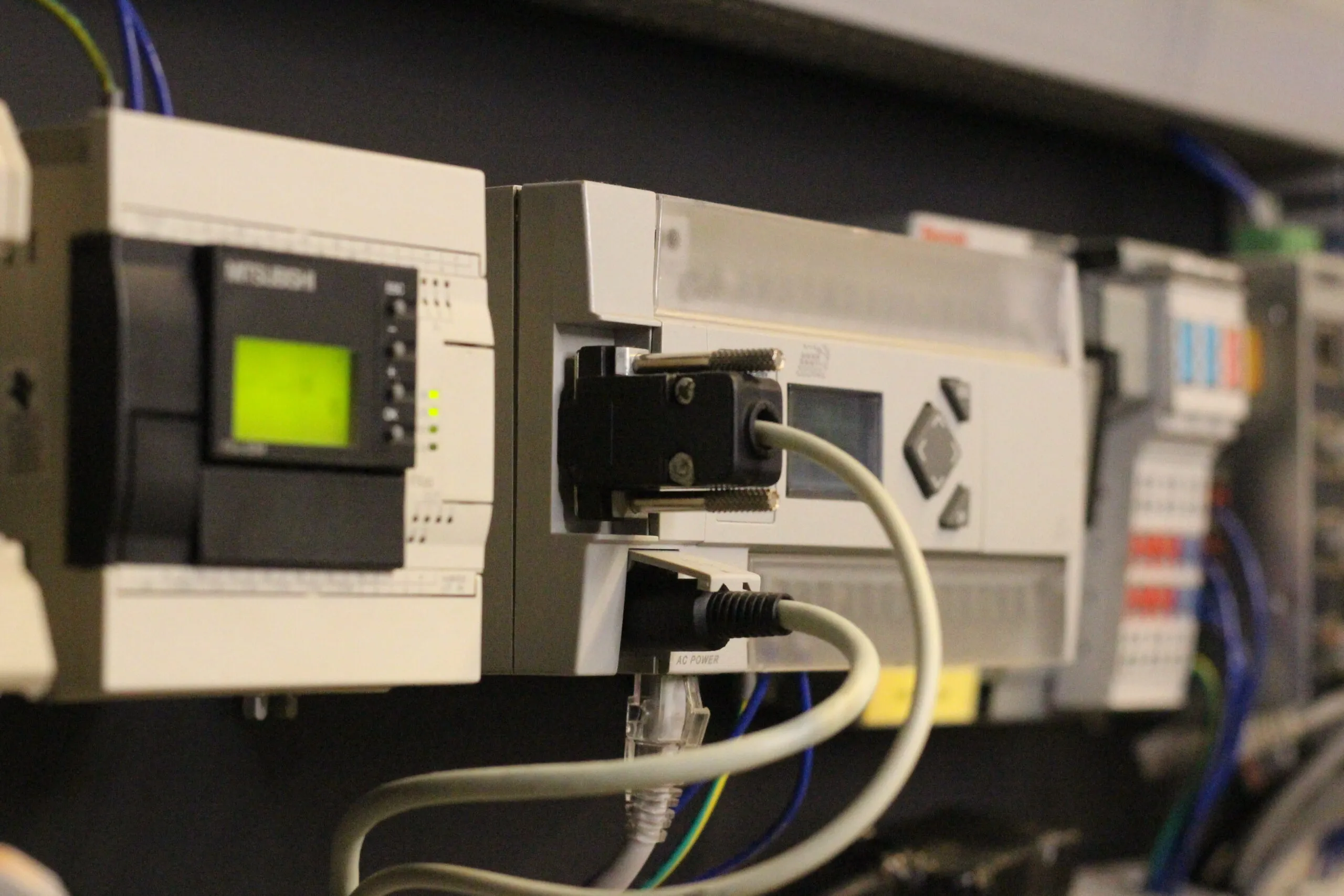
Comunicación entre Maquinaria Industrial y PLCs
Los protocolos de comunicación viabilizan la conexión de los CLPs a diversos dispositivos y sistemas, como actuadores, IHMs y otros CLPs. Operan como un conjunto de reglas que normalizan la transmisión y recepción de datos entre los elementos. El flujo de esta comunicación comprende las siguientes etapas:
- Selección del Protocolo: Inicialmente, se define el protocolo de comunicación adecuado para la aplicación. Modbus, Profibus y Ethernet/IP son ejemplos comunes.
- Configuración del CLP: El CLP se configura para emplear el protocolo seleccionado, lo que puede involucrar la instalación de módulos de comunicación específicos y la parametrización vía software.
- Adquisición de Datos Sensoriales: El CLP recolecta datos de sensores y dispositivos de entrada conectados, abarcando información como temperatura, presión y posición.
- Procesamiento de Datos: La CPU del CLP procesa los datos conforme al programa residente, tomando decisiones basadas en la lógica de control definida.
- Formato de Datos: Los datos procesados se formatean en conformidad con las especificaciones del protocolo de comunicación, asegurando la inteligibilidad para otros dispositivos en la red.
- Transmisión de Datos: Los datos se transmiten por el módulo de comunicación del CLP a la red o directamente a otros dispositivos. En redes Ethernet, por ejemplo, pueden enviarse a un servidor SCADA o sistema Historian.
- Recepción de Comandos: El CLP también recibe comandos de otros dispositivos o sistemas de control, instruyéndolo a alterar la lógica, ajustar parámetros o ejecutar acciones específicas.
- Actualización de Estados: El CLP actualiza sus estados internos y los de los dispositivos conectados con base en las retroalimentaciones recibidas.
Integración de Datos entre Diferentes Áreas en una Industria
Cada sector industrial adopta modelos de CLPs específicos, seleccionados por ambiente, complejidad y costo. Los protocolos de comunicación más comunes por sector incluyen:
- Automotriz: CANopen, debido a su baja latencia y alta confiabilidad para el control en tiempo real; y DeviceNet, basado en CAN para la interconexión de dispositivos en sistemas de control de máquinas.
- Alimenticio: Ethernet/IP, que ofrece comunicación rápida y eficiente esencial para procesos de alta velocidad de datos; y Profinet, utilizado para la comunicación en tiempo real, garantizando la sincronización precisa de procesos críticos.
- Químico: Profibus, aplicado en el control de plantas químicas por su robustez y resiliencia a ambientes agresivos e interferencias; y Modbus, ideal para la comunicación simple y robusta entre sensores y controladores industriales.
- Farmacéutico: Modbus, empleado en la comunicación entre equipos de laboratorio y sistemas de control de procesos; y Ethernet/IP, que permite la integración de sistemas de control y monitoreo en tiempo real, crucial para la calidad y el cumplimiento normativo.
- Papel y Celulosa: Profinet, fundamental para la sincronización en tiempo real de los procesos de producción; y Profibus, cuya robustez es adecuada para ambientes industriales desafiantes.
Considerando un escenario de manufactura complejo, como en la industria automotriz con sus intrincadas líneas de producción y múltiples sistemas de control, la coexistencia de diversos protocolos de comunicación es común. Los robots de ensamblaje pueden operar vía EtherCAT, los sensores de temperatura y presión vía Modbus, los controladores de motores vía CAN y los sistemas de inspección de calidad vía Profibus.
En este contexto, se vuelve esencial la implementación de una solución capaz de soportar múltiples protocolos. Este dispositivo centraliza la recolección de datos en tiempo real de todas las máquinas, independientemente del protocolo nativo. Los datos unificados se dirigen entonces a un sistema de gestión de la producción, proporcionando una visión holística de la línea productiva.
Esta integración posibilita la identificación proactiva de problemas, como desviaciones de temperatura o fallas robóticas. La fábrica, equipada con datos centralizados y analizados, puede implementar acciones correctivas precisas, como ajustes en los controladores de motores y mantenimiento predictivo.
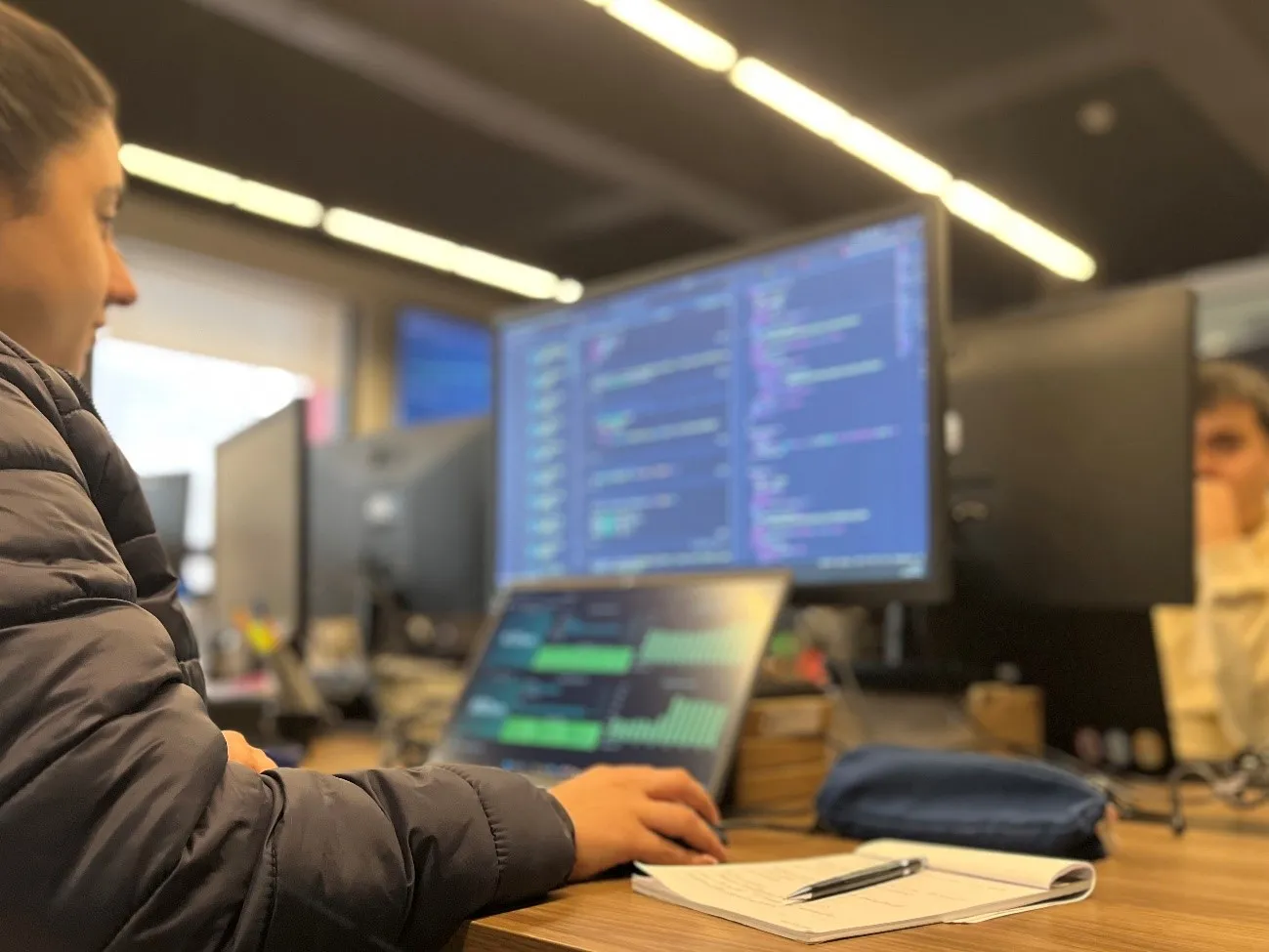
Importancia de la Compatibilidad con Diversos Protocolos
Los diversos protocolos de comunicación industriales posibilitan la conexión y comunicación de los CLPs con sensores, Interfaces Hombre-Máquina (IHMs) y otros dispositivos, siendo fundamental para la integración e interoperabilidad de sistemas de automatización.
Esta conectividad es crucial, ya que la lectura de los datos generados por la maquinaria revela insights valiosos para la operación industrial. Además del monitoreo en tiempo real de la producción, esencial para análisis de desempeño y productividad, el almacenamiento del historial de datos es igualmente indispensable. Esta visibilidad posibilita:
- Optimización de la Eficiencia Operacional: El acceso a los datos permite un mejor uso de los recursos, la reducción del tiempo de inactividad y el aumento de la productividad.
- Implementación de Mantenimiento Predictivo: Ayuda a evitar paradas no planificadas, reducir los costos de reparación y aumentar la vida útil de los equipos.
- Elevación de la Calidad del Producto: Reduce la cantidad de productos defectuosos y mejora la satisfacción del cliente.
- Disminución de Costos: El análisis de los datos recolectados auxilia en la identificación de áreas donde los costos pueden reducirse (consumo de energía, uso de materia prima).
- Mejora de la Toma de Decisiones Asertivas: Incrementa la capacidad de respuesta a los cambios en las condiciones operacionales.
La tendencia futura apunta hacia la creciente adopción de protocolos basados en Ethernet, debido a su alta velocidad y comunicación simultánea. Integrado con soluciones IoT, que permiten el almacenamiento escalable de datos en la nube, este escenario tecnológico debe impulsar la eficiencia, la seguridad y la agilidad en la adaptación operacional en los próximos años.
Conozca más sobre ST-One.